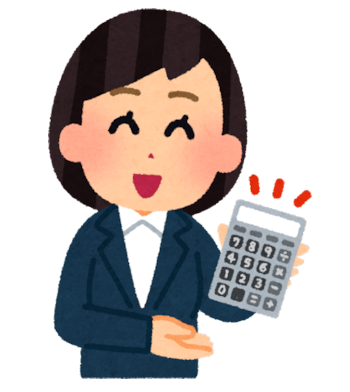
労働安全衛生法によるリスクアセスメントは危険性についても実施しなければなりません。しかしながら、化学物質の危険性についてのリスクアセスメントについての資料はほとんど見られないという事情があります。
本稿では、危険性についてのリスクアセスメントについて方法と考え方について解説しています。
- 1 最初に
- (1)背景事情
- (2)危険性についてのリスクアセスメントの困難性
- (3)リスクアセスメントが無駄になるリスク
- (4)本稿の目的
- 2 リスクアセスメントの実施方法
- (1)シナリオ抽出
- (2)リスクの見積もりの考え方
- 3 最後に
1 最初に
執筆日時:
最終改訂:
(1)背景事情
通知対象物(労働安全衛生法(安衛法)第57条の2第1項)に対するリスクアセスメントを義務化する安衛法改正は、平成28年6月1日に施行となっている。このリスクアセスメントは、有害性のみならず危険性についても行わなければならない。
有害性のうち、吸入ばく露による慢性毒性については、リスクの見積もりの具体的な手法が(他に比較すればではあるが)ある程度は確立しており、それらを活用することができる。しかし、"アクシデント性"の急性中毒や、危険性(爆発・火災)についてのリスクアセスメントの手法については、その概念(形式)は厚生労働省の「化学物質等による危険性又は有害性等の調査等に関する指針」の解釈通達である平成27年9月18日基発0918第3号「化学物質等による危険性又は有害性等の調査等に関する指針について」の別紙2「リスク見積もりの例」などにもいくつかの例が示されているものの、具体的にどうすればよいのかについて、事業者はかなり悩んでいるというのが実態である。
(2)危険性についてのリスクアセスメントの困難性
化学物質のリスクアセスメントのうち、急性中毒災害や、爆発・火災・破裂などといった、"想定外のアクシデント"によって発生する災害についてのリスクアセスメントには、次のように5つの段階が含まれる。
【リスクアセスメントの4つの段階】
- ① 対象の選定
- ② 情報の収集
- ③ 危険有害性の特定(シナリオ抽出を含む)
- ④ リスクの見積もり
- ⑤ 対策の検討
このうち、③のうちの"シナリオ抽出"と④の"リスクの見積もり"を、具体的にどのように(また"どこまで")行えばよいのかが、多くの事業者に分からないのである。
それでも、シナリオ抽出については方法がないわけではない。もちろん、化学物質の有害性や物理的特性等についての幅広くかつ専門的な知識が必要ではあるが、チェックリストを用いる等により、漏れのないようにシナリオを洗い出すことはできないわけではない。
しかし、先述したように、リスクの見積もりについては、概念的にはいくつかの手法が示されてはいるが、そのいずれの方法をとるにしても結果の重大性とその発生の可能性を判断しなければならない。ところが、結果の重大性はともかくとして、その発生の可能性を正しく評価・判断することなど、現実にはきわめて困難である。そのため、リスクの見積もりを行うことはそう簡単ではないのである。
(3)リスクアセスメントが無駄になるリスク
どのようにシナリオを抽出して、どのようにリスクを見積もるのかの具体的な手法を明確にしないまま、形だけリスクアセスメントを導入するケースがままみられる(※)。しかし、そのような事業場では、例外なく、現場ではリスクアセスメントは役に立たないと考えられている。
※ たんに形だけリスクアセスメントを行うことも、(困ったことに)できないわけではない。そして、一般論としては、形から入っていくことは、必ずしも悪いことではないのだが、形を整えることに拘泥してしまうと、全体がたんなる"壮大なる無駄"になってしまうのである。
ある事業場の年間安全衛生計画で、リスクアセスメントの目的が「労働者の安全の意識付け」に位置付けられているものを見たことがある。つまり、この事業場では、そもそもリスクアセスメントを導入しようとしている安全衛生担当者自身が、直接、労働災害の防止を目的としたものとは考えていないのである。おそらく、危険予知訓練と区別がついていないのだろう。
これでは、リスクアセスメントは、形(ポーズ)を整えるだけのために行われているというしかない。現場では、無駄と知りつつ、危険予知訓練と同様な考え方で、現実には起こりそうにもない災害を"洗い出し"て、発生したらこうなるという危害の程度を推定し、過去何十年も発生していない災害の発生頻度を"年に何回発生する"などと判断してリスクの見積もりを行っているのである。
そして、立派な書類を作成し、"結果を労働者に周知"するために詰所などに貼りだして、各部署の活動の"成果"を競い合うのだ。
(4)本稿の目的
リスクアセスメントの本来の目的は、現実に発生するおそれのある労働災害を予見し(洗い出し)て、事前に防止することである。つまり直接的な労働災害の防止の手段なのである。これは、労働者の危険予知能力を高めるための危険予知訓練などとは違うのである。繰り返すが、リスクアセスメントとは、リスクを洗い出す"教育・訓練"のために行うのではなく、"現実に起こり得る災害"のリスクを洗い出して解決するために行うのである。それ以外ではあり得ないのだ。
なお、本稿は、危険性のリスクアセスメントの考え方と銘打っているが、"想定外のアクシデント"によって発生する災害のリスクアセスメント全般について概説する。とくに、シナリオ抽出の方法及び、リスク見積もりの方法のひとつとしてのマトリクス法について詳しく解説する。
また、同時に、マトリクスを作成するための考え方についても解説する。リスクの見積もりの手法として本稿ではマトリクス法を推奨するが、マトリクス法を実施するには、まず各事業場においてマトリクスを定めなければならないからである。
なお、この内容は、本サイトの「化学物質のRAの具体的な進め方」と一部重なるが、危険性についてのリスクアセスメント手法の解説を希望する声が大きかったために、新たに稿を起こすものである。
2 リスクアセスメントの実施方法
(1)シナリオ抽出
ア シナリオ抽出の分類
急性中毒は、"想定外のアクシデント"による漏えいや、反応生成物の発生等によって発生することが普通である。また、爆発・火災・破裂等の危険性による災害も、なんらかの"想定外のアクシデント"によって発生する。なお、慢性毒性でも経皮ばく露については、"想定外のばく露経路"によって発生することが多く、"想定外のアクシデント"と同様な対応をとることになる。
リスクアセスメントの実施に当たっては、先述したように、まず危険性・有害性を特定する必要がある。そして、"想定外のアクシデント"による災害ついて、危険性・有害性を特定するとは"シナリオ抽出"をすることである。シナリオ抽出とは、災害発生のストーリーを洗い出すことである。いわば"想定外のアクシデント"や"想定外のばく露経路"を洗い出す(想定する)のである。
"想定外のアクシデント"等による災害を分類すると、想定は比較的容易だが結果はそれほど重大ではないものと、想定は困難だが結果が重大なものに分けることができる。
なお、想定が容易で結果が重大な災害は、通常の事業場では、リスクアセスメントを行うまでもなく対策は採られているであろうから、そのような災害が発生することは多くない。また、結果の想定が困難で結果が軽微な災害は、一般には発生する可能性が低く(※)、かつ結果の重大性も軽微なことからリスクは大きくないことが多い。また、何が起きるか分からないようなことをするときは、通常の事業場では、一定の対策は予防的にとっておくことが多いため、あまり発生することはないのが実際である。
※ 一般に結果の発生を予測することが困難な災害は発生の可能性は高くない。しかし、結果が重大であれば結果的にリスクは高くなるのでリスクアセスメントの必要性は低くはない。
結果の重大性 | |||
---|---|---|---|
比較的軽微 | 比較的重大 | ||
結果の想定(予想) | 容易 | Ⅲ型 | 通常、リスクアセスメントを行うまでもなく対策はとっている。 |
困難 | 通常、リスクアセスメントを行うまでもなく対策はとっている。 | Ⅰ型 |
そのため、リスクアセスメントでシナリオ抽出を行うべき主要な対象は、実質的には、上表のⅠ型とⅢ型の災害ということになる。
なお、それ以外の災害が発生したらどうするのかが気になるかもしれないが、実際には、シナリオ抽出の手法は、「結果の想定」の困難性が同程度であれば、結果の重大性の軽重にかかわらず、同じ手法で可能であるから、あまり結果の重大性の軽重は気にする必要はない。
イ シナリオ抽出の実施者
そしてⅢ型のシナリオ抽出を行うメンバーは、①現場の作業者、②職長、管理監督者などの現場を熟知しているライン管理者、③第1種衛生管理者等の社内の専門スタッフ等である。なお、衛生管理者にはリスクアセスメントのうち、技術的な事項については、必ず実施させなければならない。また、場合によっては労働衛生コンサルタントなどの社外専門家を参加させる。
一方、Ⅰ型のシナリオ抽出については、①機械設備や工程の専門家、②化学物質の専門家、③労働衛生コンサルタント等の社外専門家等によって行う。化学工業以外の中小の企業は、社外の専門家に頼らざるを得ないこととなろう。これには、コストが発生するが、一定の危険有害な化学物質を労働者に扱わせる場合には、労働災害の防止のためには、一定のコストをかける必要があるのだ。
ウ シナリオ抽出の実施方法
(ア)比較的想定の容易な災害(Ⅲ型)のシナリオ抽出
シナリオ抽出の方法は、Ⅲ型については次のように行う。
【シナリオ抽出の手順】
- ① SDS等から化学物質の危険性・有害性を洗い出す。具体的には、引火性、爆発性、経皮毒性、吸入有害性などである。
- ② 作業や機械設備の状況などから、事故のシナリオを抽出する。その具体的な例としては、チェックシートなどを用いてシナリオを抽出してゆく方法が考えられる。
- ③ 抽出したシナリオに漏れがないかをチェックする。
基本的に、Ⅲ型の災害のリスクアセスメントは、"高度な専門家でなくてもシナリオ抽出ができるような災害"について行うのである。従って、ここで最も注意すべきことは、事故が起きた後になって考えてみれば、"分かったはず"という災害発生のシナリオを見落とさないことである。そのために、チェックリストを作成することが望ましい。
なお、シナリオ抽出に当たって誤解してはならないことは、これは危険予知訓練とは違うということである。危険予知訓練では、誰かが危険な状況が存在していることを知っている。つまり教育・訓練のために、あえて"作られたリスク"を発見するのが目的なのである。
しかし、リスクアセスメントのシナリオ抽出はそうではない。そもそも誰も災害のリスクがあるとは思っていないのである。なぜなら、思っていればなんらかの対策をとっているからである。思っているにもかかわらず対策をとっていないのであれば、そもそもリスクアセスメントなどをしようとは考えないであろう。
すなわち、シナリオ抽出は、危険予知訓練とは異なって、まさに"実戦"なのであり、以下のことが重要となる。
【Ⅲ型災害のシナリオ抽出で行うこと】
- ① それまで誰も想定していなかったような事態を想定する。
- ② 気付いてはいるが見過ごしていたリスクに気付く。
このため、現場を熟知している労働者や職長などだけで行っていると、かえって、見過ごしていたリスクに気付けないという問題がある。そのため、現場を熟知している者と、部外者である専門家(第1種衛生管理者や衛生コンサルタントなどのスタッフ)の連携が重要になる。
また、ここでは、労働者のミスや不安全行為、機械設備の故障や誤動作が起こり得ることも考慮に入れなければならない。そこで、見落としのないようにチェックリストを作成する必要がある。
なお、シナリオの抽出を行うためには、①現場の状況を熟知していること、②災害発生についての知識(理論)があること、③災害の発生についての経験と感性があることの3つが重要となる。現実の現場でのシナリオの抽出には、どうしても机上の知識だけでは足りないのである。経験や感性も必要なのだ。ところが、最近では、この③が得られにくくなっているのである。
一例として、最近では少なくなっているが、かつては機械工場で自動工作機械の潤滑油などがいきなり発火して、小規模な火災が発生することがあった。このような事故が頻発していた頃は、関係者も対応方法を心得ており、事故と認識されることもなく、消火してしまったものである。しかし、最近では、事故が少なくなっているがために、予測が難しく、かつ、いったん発生するとどのように対応してよいかが分からなくて被害を大きくしてしまうことも考えられる。
リスクの予測という意味では、安全な状況が定着してきたことがかえって、困難性を増しているということを、かつての危険な状況を熟知している年齢の経営者の方は留意する必要があるかもしれない。
さて、使用するチェックリストは、リスクアセスメントの実施者の能力や、作業・機械設備の状況にもよるため、各社で作成して頂きたいが、概念的には次のようなものになろう。
① 経皮ばく露の恐れのある物質
収集資料 | 調査項目 | チェック |
---|---|---|
ヒヤリハット事例 | 事故につながる可能性 | 有・無 |
過去の事故事例 | 同種事故発生の可能性 | 有・無 |
過去に皮膚に付着した経験 | 皮膚に付着した経験の有無 | 有・無 |
作業空間中の気中濃度 | 急速に濃度が上昇する恐れ | 有・無 |
保護手袋の使用状況 | 種類・材質は適切か | 適・否 |
古いものの使用や誤った使用 | 適・否 | |
保護メガネの使用の有無 | 使用されているか | 適・否 |
(皮膚・眼への)飛散のおそれ | 液体の状態での取り扱い | 有・無 |
液体の開口容器での扱い | 有・無 | |
破損しやすい容器の有無 | 有・無 | |
物質の付着した物の取扱い | 有・無 | |
取扱い中に刺激を感じたこと | 刺激を感じたことはないか | 有・無 |
取扱い中に異臭を感じたこと | 異臭を感じたことはないか | 有・無 |
・・・・ | ||
・・・・ | ||
ここで、ヒヤリハット事例や過去の同種災害事例がある場合には、その災害については原則としてシナリオに追加するという意識が必要である。ことに、過去の同種災害が発生している場合は、同様な災害を起こしてはならないということを前提にする必要がある。
そのために、過去の災害の洗い出しと、その原因の把握を充分に行う必要がある。ここで、災害の原因が"不安全行為"や"誤操作"などとされている場合でも、たんなるルール違反や誤りと考えて、"ルールを守れば"あるいは"間違えなければ"事故は発生しないからリスクは低いなどと考えてはならないということである。リスクの判定に当たっては、"不安全行為"や"誤操作"は繰り返すと考えなければならない。
そして、対策を立てるときには、不安全行為を誘発するような事象があればそれを解消したり、そもそも不安全行為を行うことができないようにしたりすることはできないかなどまで、遡って考えることが重要である。また、誤操作についても、その原因として間違えやすい要因があればそれを解消し、場合によっては、間違えても事故が起きないような方法を考えるべきである。
なお、過去に発生した同種災害などは、その化学物質だけではなく、経皮毒性のある別な物質の災害などの事例も参考にする必要がある。
その他、化学物質が皮膚に付着する可能性を洗い出す。一例として、福井県の化学工場で発生したo-トルイジンによる膀胱がんは、保護手袋を再生有機溶剤で洗浄したことが原因ではないかと考えられている。すなわち、保護手袋の外側に付着していたか、再生有機溶剤中に含まれていたo-トルイジンが、洗浄したことによって手袋の内側に付着し、これが労働者に経皮ばく露したのではないかと考えられているのである。このような災害をなくすためには、ばく露の経路を徹底的に洗い出す必要があるだろう。
② 吸入毒性のある物質
収集資料 | 調査項目 | チェック | |
---|---|---|---|
ヒヤリハット事例 | 事故発生の可能性 | 有・無 | |
過去の事故事例 | 同種事故発生の可能性 | 有・無 | |
比較的多量の漏えいの恐れ | 有・無 | ||
誤操作による漏えい | 漏えいの恐れの有無 | 有・無 | |
開口部からの漏えい | 漏えいの恐れの有無 | 有・無 | |
容器破損による漏えい | 漏えいの恐れの有無 | 有・無 | |
取扱い中に異臭を感じたこと | 異臭を感じたことはないか | 有・無 | |
局所排気装置の使用の有無 | 局所排気装置の使用の有無 | 有・無 | |
・・・・ | |||
・・・・ | |||
ここで、例えば「局所排気装置の使用の有無」について、局所排気装置を作動させずに化学物質を取扱う恐れがないかなど、ヒューマンエラーについても検討する必要がある。もしおそれがあると判断する場合は、照明装置を点灯させた場合は局所排気装置が自動的に起動するようにする(停止は照明装置と連動させない)、作業時間になると局所排気装置が自動で起動するようにする、風車を取り付けて局所排気装置の作動状況を"見える化"するなどの対策をとることが考えられる。
なお、あくまでも、ここで問題とするのは"慢性ばく露"ではない。また、Ⅲ型災害なので、異常な事故による高濃度の漏えいのうち、比較的、想定のし易い事故を洗い出すのである。
ガラス製の容器を運搬中に落として割れるおそれはないかとか、大型容器から小型の容器や機械設備に移し替えるときに発生した蒸気にばく露することはないか、誤って開放すべきでない容器の蓋を開放してしまう可能性はないかなど、通常の労働者が思いつくようなアクシデントを洗い出すことがここでも目的なのである。
③ 単純窒息性のあるガス
収集資料 | 調査項目 | チェック |
---|---|---|
ヒヤリハット事例 | 事故発生の可能性 | 有・無 |
過去の事故事例 | 同種事故発生の可能性 | 有・無 |
使用量 | 酸素濃度の低下するおそれ | 有・無 |
誤操作等による漏えいの恐れ | 漏えいの恐れの有無 | 有・無 |
ガスの比重とピットの有無 | ガスの比重は空気より重いか | 重・軽 |
ピット内での作業はあるか | 有・無 | |
ピット内に警報機はあるか | 有・無 | |
ピット内に換気扇はあるか | 有・無 | |
一人作業はあるか | 有・無 | |
・・・・ | ||
・・・・ | ||
空気よりも重い単純窒息性ガスを大量に使用する場合には、酸欠についてのリスクを判断する必要がある。とりわけ単純窒息性のガスを多量に用いる装置等の下部にピット等がある場合は注意が必要である。
酸欠防止のためには、ガスを漏らさないことがリスクの低下のために重要である。また、"ガスの漏れるおそれの可能性"の大きさを評価しなければリスクアセスメントはできないことになる。しかし、対策にそれほどのコストがかからず、かつ発生すると被害が大きい酸欠事故のような災害については、リスクアセスメントの実施も重要ではあるが、同時に、リスクアセスメントから離れて、"あるものは漏れる"と考えることも必要である。
最近では、極めて小型の携帯用の警報機も開発されている。これを労働者に持たせて、酸素の濃度が18%以下になったときに動作しておくようにすれば、リスクをある程度下げることが可能である。また、一人作業をできるだけなくすこともリスクの低下につながる。
また、ピット内に入るときは必ず換気扇を動かすようにすることでもリスクを減少させることができる。ただし、この場合は、換気扇の位置や能力ばかりではなく、スイッチの入れ忘れなどのヒューマンエラーについても考慮する必要がある。
④ 引火性のある液体・ガス
収集資料 | 調査項目 | チェック |
---|---|---|
ヒヤリハット事例 | 事故発生の可能性 | 有・無 |
過去の事故事例 | 同種事故発生の可能性 | 有・無 |
温度が引火点に達する恐れ | 温度が引火点に達する恐れ | 有・無 |
着火源の有無 | 着火源の有無 | 有・無 |
誤操作による漏えいの恐れ | 誤操作の恐れの有無 | 有・無 |
・・・・ | ||
・・・・ | ||
引火性の液体やガスによる火災災害のシナリオ抽出は、①蒸気・ガスの漏えい、②液体の温度の上昇、③着火源の存在などによって判断することになる。すなわち、①から③までの発生が起こることを予測して、シナリオを組み立てるのである。蒸気・ガスの漏えいや、液体の温度の上昇については、誤動作や想定外の事態も考慮しなければならない。
また、ヒューマンエラーや設備の誤作動によって液体や蒸気などが漏えいして、これに引火するようなケースも考慮する必要がある。例えば、スプレー作業などでは、局所排気装置などが作動しないことによる漏えいなども考慮しなければならない。さらに、塗布作業でも、想定外の事情により塗布される物の温度が上昇することなども考慮する必要がある。最近ではあまり聞かないが、かつては、戸外で金属製の物に塗装していて、金属が日光によって温度が上昇し、何かの着火源によって発火するという事例もあったのである。
卑近な例ではあるが、最近、ある事業者の方から伺ったのだが、建物の入り口に手を消毒するためのアルコール噴霧器が置いておいたら、これが引火燃焼したというのだ。着火源が何かまではお伺いできなかったが、なにかの着火源が近くにあったのであろう。もちろん、それほど大きな災害にはならないのだが、引火性の液体を噴霧するのであるから、消毒剤の近くに着火源があればこのような燃焼することは予測ができないわけではないだろう。
⑤ 爆発性のある蒸気、ガス、粉じん
収集資料 | 調査項目 | チェック |
---|---|---|
ヒヤリハット事例 | 事故発生の可能性 | 有・無 |
過去の事故事例 | 同種事故発生の可能性 | 有・無 |
着火源の有無(※1) | 着火源の有無 | 有・無 |
濃度が爆発限界に達する恐れ(※2) | 濃度が爆発限界に達する恐れ | 有・無 |
化学反応による爆発の恐れ | 誤操作による異常な化学反応 | 有・無 |
・・・・ | ||
・・・・ | ||
※1 最小着火エネルギー以上の着火源がないかの有無を調べる。なお、水素ガスやメタンガスなど最小着火エネルギーの低い物質の場合、着火源は常に「有」と判断する。
※2 ガス体容器の開口部の誤操作による気中濃度の上昇、粉じんの舞い上がりによる気中濃度上昇などの可能性がないかをチェックする。
ここで問題とするのは、あくまでも単純な漏えいや粉じんの舞い上がりによって爆発限界に達したガス等に着火して爆発する事故である。複雑な化学反応によるものは、次項で検討しなければならない。
爆発というと、爆燃性のものの存在、酸素の存在、着火源の3つを問題にすることが多いが、物質によっては酸素がなくても爆発するし、着火源がなくても自然発火するものもある。かつて宮崎県で発生したIC工場の排気ダクト火災では、シランガスが自然発火したことが原因である。このような災害は、次項のⅠ型に属するものが多いだろうが、現場に専門的な知識と能力を有する者がいるのであれば、判断しておく必要がある。
なお、廃棄有機物などを扱っている場合などでは、メタンガスなどが自然発生するリスクも考慮する必要がある。さらに、自然発生するガスについては爆発のみならず、密閉容器内での圧力の上昇による破裂についても考慮する必要がある。実際に、廃てんぷら油を入れていたドラム缶が破裂して、死亡災害となった例も存在している。
(イ)比較的想定の困難な災害(Ⅰ型)のシナリオ抽出
一方、Ⅰ型については、専門家を擁する一定規模以上の大企業を除けば、専門家に頼らざるを得ない面がある。一般の中小の企業では、自らリスクアセスメントが可能なのは、比較的シナリオ抽出の容易なⅢ型の事故に限られると考えるしかない。
ある程度、複雑な化学反応などによって発生する災害は、専門家による(すなわちコストをかける)必要があるということを理解するべきである。
機械設備の異常な動作によるプラント災害などは、その設備の専門家や化学の専門家によって、様々な状況を想定し、それらについてのチェックリストを作成して、ひとつひとつの状況についてのシミュレーション(思考実験)を行ってみることが現実的であろう。
この場合、想定された状況についてのみ検討するのではなく、異常な用いられ方をすることも考慮に入れるべきである。また、思い込みによって状況を見落とすことがないよう、ときにはその機械設備の設計等にかかわっていない専門家や部外者を検討に参加させることも必要である。
(2)リスクの見積もりの考え方
ア 様々なリスク見積もりの手法
"想定外のアクシデント"による災害のリスクを見積もる方法としては、先述した厚労省の指針の解釈通達の別紙2「リスク見積りの例」には、マトリクス法、及び、数値化法が示されている(※)。
※ なお、厚労省のWEBサイトに公開されているいわゆる厚生労働省版コントロール・バンディングは、危険性(爆発・火災・破裂)や急性中毒のリスクアセスメントに用いることはできない。
なお、枝分かれ法を示している文献も一部にあるが、枝分かれ法は機械設備等を設計するときなどに用いられるものであり、"想定外のアクシデント"による労働災害のリスクを見積もる方法としては、やや使いずらい面もある。また現実にもあまり用いられることもないから本稿では考慮しない。
(ア)マトリクス法の概念
マトリクス法は、結果(危害)の重大性と災害発生の可能性から、直接的にリスクを見積もる方法である。この方法をごく単純化して概念的に示せば、次のようになる。
【マトリクス法の概念】
- ① まず次のようなマトリクスを作成しておく(※)。
- ② ある災害発生のシナリオについて、その災害が発生した場合の危害の大きさと、その災害が発生する可能性を推測する。
- ③ 推測した危害の大きさと、その災害が発生する可能性から、マトリクスを用いてリスクのレベルを推定する。例えば危害の重大性が"中"程度で、災害発生の可能性が"小"ならリスクのレベルは"Ⅰ"となる。
※ あくまでもこのマトリクスは概念的なものであり。各セルの数値には意味はない。実際には、もっと複雑なものが使用される。
危害の重大性 | ||||
---|---|---|---|---|
大 | 中 | 小 | ||
災害の発生の可能性 | 大 | Ⅴ | Ⅳ | Ⅲ |
中 | Ⅲ | Ⅱ | Ⅰ | |
小 | Ⅰ | Ⅰ | Ⅰ |
リスクレベル | リスクレベルの意味 | |
---|---|---|
Ⅴ | 高 | 耐えられないリスクレベル。 |
Ⅳ | 早急に対策をとる必要がある。 | |
Ⅲ | 中 | 必要に応じて対策をとる。 |
Ⅱ | 状況に応じて対策をとる。 | |
Ⅰ | 低 | 容認できるリスクレベル |
ここでの最大の課題は、マトリクスをどのように定めるかと、災害発生の可能性をどのようにして推測するかである。
(イ)数値化する方法
また、リスクの見積もりの手法のひとつとして、数値化する方法(掛け算法や加算法)が用いられることがある。これは、リスクは、概念的には"結果の重大性"と"発生する可能性"の積で表すことができる。そこで、結果の重大性の大きさと発生の可能性を推定し、この2つを掛け合わせることでのリスクの大きさを判定しようという手法である。
具体的には、次のような方法である。
【数値化法(掛け算法)の概念】
例えば、結果の重大性と発生する可能性の区分を、予め以下のように定めておく。
結果の重大性 | 重大 | 大 | 中 | 軽微 |
7,500 | 800 | 40 | 2 |
発生する可能性 | 大 | 中 | 小 | 極小 |
50 | 10 | 0.2 | 0.001 |
そして、ある災害のシナリオが、現実化する可能性が"中"程度で、その重大性が"大"だとすると、そのリスクを
リスクの大きさ =
と判断する。
この方法は、リスクの本来の定義(結果の重大性と発生する可能性の積)をそのまま数式化しているので、概念的に分かりやすい。しかし、リスクの評価の際に"結果の重大性"と"発生する可能性"の大きさを正しくスケール化(数値に当てはめる)することができなければ、判定したリスクの大きさも正しく評価することはできないことになる。
また、掛け算法では、概念的に"結果の重大性"と"発生する可能性"の大きさをそのまま数値にするので、得られるリスクの数値の大きさの大小の幅が極端に大きくなってしまうので、やや使いづらいという指摘がある。そこで、これを(概念的に)LOGスケールで表したものが足し算法である。ある調査によると我が国では最も多く用いられている。
具体的には次のような方法である。
【数値化法(足し算法)の概念】
この方法では、例えば、結果の重大性と発生する可能性の区分を、予め以下のように定めておく。
結果の重大性 | 重大 | 大 | 中 | 軽微 |
4 | 3 | 2 | 1 |
発生する可能性 | 大 | 中 | 小 | 極小 |
4 | 3 | 2 | 1 |
そして、ある災害のシナリオが、現実化する可能性が"中"程度で、その重大性が"大"だとすると、そのリスクを
リスクの大きさ =
3(結果の重大性)+3(発生する可能性) = 6
と判断するわけである。
ただ、この場合は、リスクの判定のときに、結果の重大性と発生する可能性を感覚的に掴みにくいという難点がある。また、上記の例では、結果の重大性が"重大"だと、発生する可能性が"極小"でもリスクは5になってしまい、一方、結果の重大性が"軽微"だと発生する可能性が"大"でもリスクの大きさは5にしかならない。すなわち、予め、適切な数値化をするのがかなり難しいという難点がある。
なお、足し算法は、掛け算法の数値をLOGスケールで表しているので、発生の可能性にはマイナスの値があってもよさそうに思えるのだが、なぜかわが国では、マイナスにすることは多くない。おそらく、発生の可能性の判断をするにあたって、マイナスという数値が分かりにくく、リスクアセスメントの実施者が正しい判断ができなくなるおそれがあるからだと思われる。
イ なぜマトリクス法を推奨するのか
(ア)数値化する方法の問題点
数値化する方法は、結局のところ、結果の重大性と災害発生の可能性に対して数値を付与し、マトリクスの各カラムにそれぞれの積や和を当てはめているわけである。足し算法の場合は次のようになる。
ここだけを定める
【足し算法】 | 危害の重大性 | |||||
---|---|---|---|---|---|---|
重大 | 大 | 中 | 軽微 | |||
4 | 3 | 2 | 1 | |||
災害の発生の可能性 | 大 | 4 | 8 | 7 | 6 | 5 |
中 | 3 | 7 | 6 | 5 | 4 | |
小 | 2 | 6 | 5 | 4 | 3 | |
極小 | 1 | 5 | 4 | 3 | 2 |
先述したように、マトリクス法が、マトリクスの各カラムを定めるのに対して、数値化法は自由度が低いため、より適切な数値を定めることが難しいのである。
例えば、結果が重大であっても可能性が低ければ、リスクは容認できると考える必要がある。やや極端な例だが、海外出張を命じるときのリスクを考えてみよう。海外出張では、ほとんどの場合、航空機で出張する。そして、航空機事故に遭遇する確率は、近年ではきわめて低いが"ゼロではない"すなわち可能性はあるだろう。危険源(ハザード)が存在する限り、リスクゼロはあり得ないのである。また、最近ではテロに遭遇する可能性もないわけではない。そして、航空機事故やテロへの遭遇では、死亡する危険性が高い。
そこで、海外出張をするときのリスクを上記の表で判定すると、危害の重大性が"重大(=4)"で可能性が"極小(=1)"となって、リスクレベルは5(=4+1)になる。しかし海外出張のリスクは、常識的には容認可能なものであろう。であればリスクの値が"5"のリスクレベルは"容認できる"と判断しなければならないことになる。しかし、そのように考えると、今度は、危害の程度が"中"で発生の可能性が"中"のときもリスクレベルは"5"なので容認できることになってしまう。これはおかしい。すなわち、この表の数値は適切ではないのである。
そこで、可能性の数値をいじっていよう。なお、この場合、危害の重大性の数値をいじるとすると、重大な災害(死亡災害)と軽微な災害(不休災害)の差を小さくしなければならなくなるが、それではやや通常の感覚からかけ離れたものになってしまうだろう。
【足し算法】 | 危害の重大性 | |||||
---|---|---|---|---|---|---|
重大 | 大 | 中 | 軽微 | |||
4 | 3 | 2 | 1 | |||
災害の発生の可能性 | 大 | 8 | 12 | 11 | 10 | 9 |
中 | 6 | 10 | 9 | 8 | 7 | |
小 | 2 | 6 | 5 | 4 | 3 | |
極小 | 1 | 5 | 4 | 3 | 2 |
これで、やや現実的な結果が出せる値となっている。ただ、まだおかしなところが出てくるようだ。
ところが。マトリクス法では、マトリクスの各カラムに直接数値を入れるために、適切なマトリクスを作成することが容易にできるのである。であれば、あえて数値化法を用いる必要はないのではなかろうか。
(イ)マトリクス法に対する問題点の指摘とそれへの反論
数値化法であれば、要素を3つ以上にすることができるが、マトリクスではそれができないという問題が指摘されることがある。例えば数値化法では、発生する可能性を、「作業の頻度」、「作業中に危険が生じる頻度」「危険が生じたときにこれを避けることができない確率」などに分解することができるが、マトリクス法ではこれができないというのだ。
このような批判の背景には、我が国でのリスクアセスメントでは、加算法の3要素法が最も多く用いられているという調査結果もあるようだ。
しかしながら、マトリクス法では要素を増やせないというのは誤解にすぎない。マトリクス法でも、マトリクスを複数個用いる(複数の段階を経る)ことにより対応は可能だからである。
この場合、の2つのマトリクスを用いればよいだけのことであろう。
- ① 「作業の頻度」と「作業中に危険が生じる頻度」のマトリクス
- ② 「①のマトリクスの結果」と「危険が生じたときにこれを避けることができない確率」のマトリクス
具体的に言えば、以下のような二つのマトリクスを作成しておき、例えば、作業の頻度が"大"、作業中に危険が生じる頻度が"中"、危害の重大性が"中"なら、以下のようにして、リスクレベルを"Ⅳ"と判定できるのである。なお、この図はたんなる概念図であり、このマトリクスの使用を奨励するものではない。
作業の頻度 | ||||
---|---|---|---|---|
大 | 中 | 小 | ||
作業中に危険が生じる頻度 | 大 | 5 | 4 | 3 |
中 | 4 | 3 | 2 | |
小 | 3 | 2 | 1 |
危害の重大性 | ||||
---|---|---|---|---|
大 | 中 | 小 | ||
災害の発生の可能性 | 5 | Ⅴ | Ⅳ | Ⅲ |
4 | Ⅴ | Ⅳ | Ⅲ | |
3 | Ⅳ | Ⅲ | Ⅱ | |
2 | Ⅲ | Ⅱ | Ⅰ | |
1 | Ⅰ | Ⅰ | Ⅰ |
また、要素を複数に分ければ結果が正確になるというものでもないだろう。実際にやってみると分かるが、たんに誤差が複数倍になるだけということが多いのである。
そこで、私としては、リスクの見積もりにはマトリクス法により、かつ要素の数は2要素とすることをお勧めしたい。
ウ マトリクスの定め方
マトリクス法を使用する場合のよくある間違いとして、研修会などで教わったマトリクスをそのまま使用するケースがある。残念ながら、現時点では労働災害のリスクアセスメントについて用いられるマトリクスで、十分な検討が行われているものはそれほど多くはない。研修会などで使用されるものの多くは、たんに概念を示したものにすぎないものと考えた方がよい。
マトリクスは、必ず自社で検討して作成する必要がある。ここでは、マトリクスを実際に作ってみよう。マトリクスを作成するにあたっての基本的な考え方を示せば、以下のようになる。
- ① あまり細かく区分を分けても、どの区分に分類するかの判断ができなくなる。4区分か5区分程度が現実的である。
- ② 発生可能性については、最近の個別企業では重大な災害はほとんど発生していないことから、可能性の高いところで区分を分けると、すべてのシナリオで、可能性が最小の区分になってしまう。そこで、かなり可能性の低いところで区分した方がよい。
- ③ 死亡災害についても、容認可能という区分を設けた方がよい(※)。下記の暫定的なマトリクスでは5,000年に1度の発生程度については容認可能とした。これについては2,000年に1度、10,000年に一度などの意見もある。判断の分かれるところだろうと思う。
※ 死亡災害については、本来あってはならないものであり、容認できるというリスクレベルがあるのはおかしいのではないかと思われるかもしれない。しかし、これはこうしないと、かえってリスクに応じた対策をとるという考え方に反することになるのである。これについては、本サイトの「労働安全衛生活動の目的を見失うな」を参照して頂きたい。
ここで、暫定的な数値を入れたマトリクスを仮に作成してみよう。なお、これはあくまでも説明のために暫定的に作成するものであり、このマトリクスの使用を推奨するものではないのでご留意頂きたい。また、公衆災害や消費者災害のリスクアセスメントを行う場合には、リスクの判定はこの表よりも1桁程度厳しいものにしなければならないと考える(※)。
※ 労働災害のリスクの判定を、公衆災害や消費者災害よりも"ゆるく"判定することについては議論があるところだと思う。しかし、私自身は、現時点における状況を前提にする限り、これらを同列に扱うことはできないのではないかと考えている。なお、動物実験で得られたNOAELなどからヒトで許容される濃度を算定するとき、労働者の場合は"種内差"を考慮しないが、このこととは別な話である。
参考までに、公衆災害については、英国安全衛生庁(HSE)のT.E.マジソン「化学工業における重大事故の制御について」(2009年度第二回公開セミナー関連)は、1人死亡のリスクについて10-6~10-8/回/年のときに「受け入れ可能」としている。なお、消費者災害のリスクアセスメントについては、R-Map実践ガイダンス(日本科学技術連盟の研究会)、MIL-STD-882D(米国国防総省調達企画)などが参考になる。
ここで、"発生可能性"は最も大きなものでも、5年に1回とした。小さすぎると思われるかもしれないが、これは工場全体での災害発生件数ではなく、あるひとつのシナリオの発生件数である。今の日本の工場の災害の状況から判断して、これ以上、頻度の高いものを考えてもあまり意味はないように思える。もちろん、いくら軽症災害(不休災害)でも1週間に1度程度発生するようなリスクがあれば、そのリスクレベルは"Ⅴ(=リスクの低下措置をとるまで作業停止する)"又は"Ⅳ(ただちに対策を講じる)"とするべきではある(※)。
※ したがって、実際にそのようなリスクがあると判断されるような工場であれば、マトリクスのうち、最も大きな"発生可能性"の区分は「きわめて大(1週間に一度)」などとしなければならない。しかし、そのようなリスクがあるのであれば、(普通の会社であれば)リスクアセスメントなどするまでもなく対策をとっているのではなかろうか。
危険又は健康障害の程度(重篤度) | |||||
---|---|---|---|---|---|
死亡 | 後遺 障害 |
休業 | 軽傷 | ||
危険又は健康障害を生ずるおそれの程度 (発生可能性) |
起こり得る (5年に1回) |
Ⅴ | Ⅴ | Ⅳ | Ⅲ |
可能性はある (10年に1回) |
Ⅴ | Ⅳ | Ⅲ | Ⅱ | |
考えにくいが可能性がある (50年に1回) |
Ⅳ | Ⅲ | Ⅱ | Ⅰ | |
きわめて可能性は低い (500年に1回) |
Ⅲ | Ⅱ | Ⅰ | Ⅰ | |
通常、あり得ない (5,000年に1回) |
Ⅰ | Ⅰ | Ⅰ | Ⅰ |
このマトリクスによって得られたリスクレベルから、下記表によって、優先度を求める。
リスク | 優先度 | |
---|---|---|
Ⅴ | 高 | リスクの低下措置をとるまで作業停止する。 |
Ⅳ | 直ちに対策を講じる。 | |
Ⅲ | 中 | 速やかにリスク低減措置を講ずる。 |
Ⅱ | できるだけ早くリスク低減措置を講ずる。 | |
Ⅰ | 低 | 必要に応じて対策をとるか、保険をかける。 |
また、死亡災害が5,000年に一度程度の発生であれば容認できるとしたが、これについては異論のあるところだと思う。ただ、2,000年に一度としたり、10,000年に一度としたりしてみても、実際にそれほど正確な算定ができるとも思えないので、さして意味のない議論ではある。
重要なことは、死亡災害であっても"容認できる"というレベルを設定することである。これを設定しておかないと、さきほどの例の海外出張まで、容認出来ないということになりかねないのである。そうなると、現場では、海外出張を禁じるわけにはいかないので、リスクアセスメントの結果をごまかすか、"リスクはない"などとしてリスクアセスメントを行わないようになってしまう。海外出張くらいなら問題はないが、実際に発がん性のある化学物質や、致死性のある物質を使用している場合、現実にはリスクゼロはあり得ないのである。死亡災害について"容認できる"というレベルを設けることにより、衛生委員会など、労使の自治の中で、どこまでリスクを下げれば容認できるのかを検討して合意することが可能になるのである。
また、リスクがあるからこそ、保険をかけたり事故があった場合の対応を整えたりすることも可能になるのである。わずかでも死亡するリスクがあることは許されないなどと考えると、海外出張を命じるときには、海外出張で死亡するリスクはないとの建前を維持するしかなくなり、保険を掛けたり、災害が発生したときの対応(緊急連絡先の整備など)を整えておくことさえできなくなってしまうのである。
エ 災害発生の可能性の判断の基準
(ア)災害発生の推定方法
さて、前記のマトリクスでは、"発生可能性"に数値を入れているが、これはイメージをつかみやすいようにするためである。例えば"可能性がある"などとするだけでは意味が不明瞭になるのである。可能性があるというのを"ゼロではない"と理解すれば、富士山が噴火するリスクもゼロではないし、宇宙人が攻めてくるリスクさえゼロとはいえないであろう。"可能性がある"だけでは意味が分からないのである。
もちろん、現実には、災害発生の可能性を数値で正確に表すことなどできるものではない。仮にできたとしても、かなりの数になるかもしれないリスクのすべてについて、発生の可能性を計算することなど、現実的でもなければ、意味があることでもない。ヒューマンエラーの頻度を推定してみたところで、どこまで正確な数値になっているかなど、分かりはしないのである。
(イ)Ⅲ型災害の発生の頻度の推定方法
【Ⅲ型災害の発生の頻度の推定方法】
- ① 参加者全員が、発生頻度について、マトリクスに示された発生頻度の数値を見て、発生頻度の区分がどこになるかについての判断をする。
- ② 最も大きな区分評価をした者に、その理由を説明させる。
- ③ 是認で検討して、その理由が納得できると判断できれば、その区分を採用する。
- ④ その理由が納得できなければ、次に大きな区分評価をした者に、その理由を説明させる。
- ⑤ 以下、③、④を繰り返す。
この方法では、多数決に比してリスクが高くなる傾向がある。しかし、多数決ではリスクの発生について、多数派が誤った理解をしていると、結果的にリスクも誤ったものになってしまう。少数者が正しくリスクを判断していることもあるため、このような手法を用いるものである。
(ウ)Ⅰ型災害の発生の頻度の推定方法
一方、Ⅰ型災害については、結果が重大なものが多いため、対策にどこまでコストをかけるべきかが重要な経営判断となる。そのため、発生頻度もⅢ型に比較すると正確に算定する必要がある。
このことの故にも、専門家による必要があるのだが、基本的に、過去の事故の事例などから判断するようなことになろうが、専門家に任せきるのではなく、最終的には事業者(又は事業者から指示を受けた者)が判断するべきであろう。
3 最後に
最後になるが、リスクアセスメントとは、結局は、災害の発生を想定(シナリオ抽出)してその結果を避けるための手段である。災害の発生を想定できなければ、意味はないのである。
しかしながら、アクシデントによる災害のリスクアセスメントとして、オフィシャルな方法が存在しているわけではない。あくまでも、ここに示した手法は概念的なものにすぎない。
本稿を参照して、各事業場で独自の対応を取って頂きたい。